IoT導入による生産性向上への取り組み
武州工業株式会社 代表取締役 林英夫氏
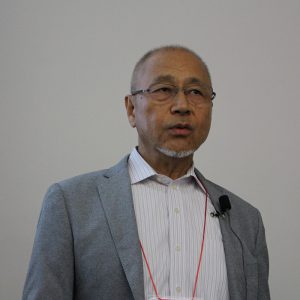
あくまでシステム化は手段、人が大事
「ITやIoTは使うと監視が過ぎてブラックになってしまう会社もある。そうではなく働く人を幸せにするような使い方をすることが武州工業の特徴だ」
林氏はまず武州工業のモノづくり「職人のモノづくりに学ぶ」という理念と、それを実現する特殊な生産体制について語った。
まずは、優れた職人は自ら適した道具を作ることから、自社設備の開発も内製している。レーザー加工機や端末機も内製化していてすでに18機作ったという。コストは購入するより低く、自分たちの製造に適した設備は作業効率を向上させた。
次に「人に任せる」ということで多能工の育成を行っている。アルミロー付という難しい作業があるが、入社時に必修で学ぶという。最初に難しいことができるようになれば、他は簡単に感じるからだ。そして、属人化させないように多能工を育成するため、武州庵という青梅の研修施設での研修やQC検定への全員合格を目指しているなどいくつもの施策を行っている。
そこで特徴となる生産方法が「1個流し生産」だ。通常の製造工程では1人の技術者が1つの工程しか担当しない。しかし武州工業では1人の技術者が複数の工程を担う。それにより、工程内品質保証が可能となり、高品質で効率的な生産が可能となる。そのような特殊な生産体制についてほかの企業からの関心は高く、毎日のように見学者が来る。
現場で3年積んだ経験が武州工業に最適なシステムを作る
多能工となり一人でいくつもの工程を担当することで一人一人がフランチャイジーみたいなものとなり自律性が生まれる。それを支えるしくみが「武州マネジメント統括システム BIMMS」だ。製造POSシステムとして日々決算のできる仕組みとなっている。その開発方法も独特で、プログラムができる人を採用して、3年現場に入ってもらって、班長クラスになってから開発を始め、作り出してきた。
リアルタイムで情報を共有するBIMMSでは、毎日棚卸をし、出退勤、生産指示、倉庫在庫管理、工程不良管理、状況分析、品質管理、生産実績管理を一元的に管理している。240台稼働中(タブレット170台)で運用していて、だれがいつ何をやったか常時記録に残る。
「記録に残ると人間は嘘をつかない。紙に記録するのと異なり、改ざん、ねつ造が縁遠くなる。
また、システムで入出庫の入力のミスをチェックすることにより、現物棚卸とデータがほぼ合う。バタバタしたのは2か月くらいであとはデータも正しくなり安定的に運用している」
本当に適切な情報提供するために
その効果はどのようなものがあるか。
データを裏付けに活動することで、納期・購買管理への効果があった。受注は一定でなく山と谷があった。しかし、データから平準化して当たりを付けて製造していくことで、社内的には対応できた。そのうちにお客様が武州の安定的な納品に気付き、過剰に在庫を持たなくともよいと、平準化量で受注できるようになった。協力メーカーともデータ連携を行い、発注レスで富山の置き薬のように持ってきてもらうという。データを共有することでお互いが一歩早く動けるメリットがある。
品質においてもトレーサビリティの情報を元に標準偏差を設定し、設定値を切るとアラートを出す。製品が安定的でなくばらつきが増えたことを管理者に通知し、対策が講じられるようになった。逆に、出来の良い部分については検査を減らしたりもできる。
「気付くべき人に気付くべきタイミングで適切な情報をリアルタイムで提供する。これがIT化の強み」
と林氏は自信を持って語った。
さらにトレーサビリティについては自社でシステム化する事でISO9001を卒業した。活動自体はシステム上で行っている。お客様が求める品質情報を欲しい時に欲しい内容を自由に引き出せる仕組みを用意している。本質を理解しているからこその取り組みだ。
生産性向上のためのIoT活用については「生産性見え太くん」を開発した。スマートフォンの歩数計の機能を使って、機械に取り付けデータ収集し、ペースメーカーとして自動的にデータを記録する。そして、見え太君解析モードで、機械の停止理由入力により解析を行う。昭和の機械に取り付けてIoTができてしまうことが特徴だ。これにより、停止している時間が明らかになり、理由を入力させることで、生産性20%向上した。
中小の日本の製造業を巻き込む未来への展望
「ITそしてIoTの時代は、会計、品質管理、生産管理などバラバラに入力していたものがリアルタイムで情報を貯めておき、それを活用するという時代だ。中小企業庁が次世代企業間データ連携調査事業コンソーシアムにも参加した。2018年12月から金融のEDIであるZEDIが動き出す。BIMMSのデータの連携も構想している。工程間の在庫、品質、検収情報を載せて、皆で使うことでシームレスな情報連携が実現できるのではないか。トヨタ圏では実証実験も始まっていて、ISDNの終わる2024年には実現するのではないかと考えているがその前に過渡期がある。システムは人が買ってくれば使えるが、活用に至るには人間が変わらなければならない。人が変わるためにスモールスタートで良いデータを残すこと、それによる恩恵を感じられることが大事だ」
と林氏は締めくくった。
田口雅美(BSIA運営委員・株式会社キテラス)